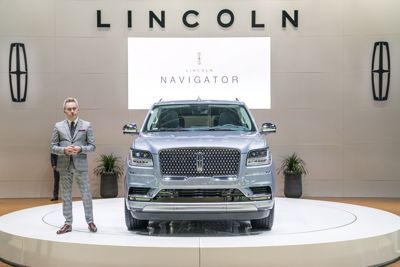
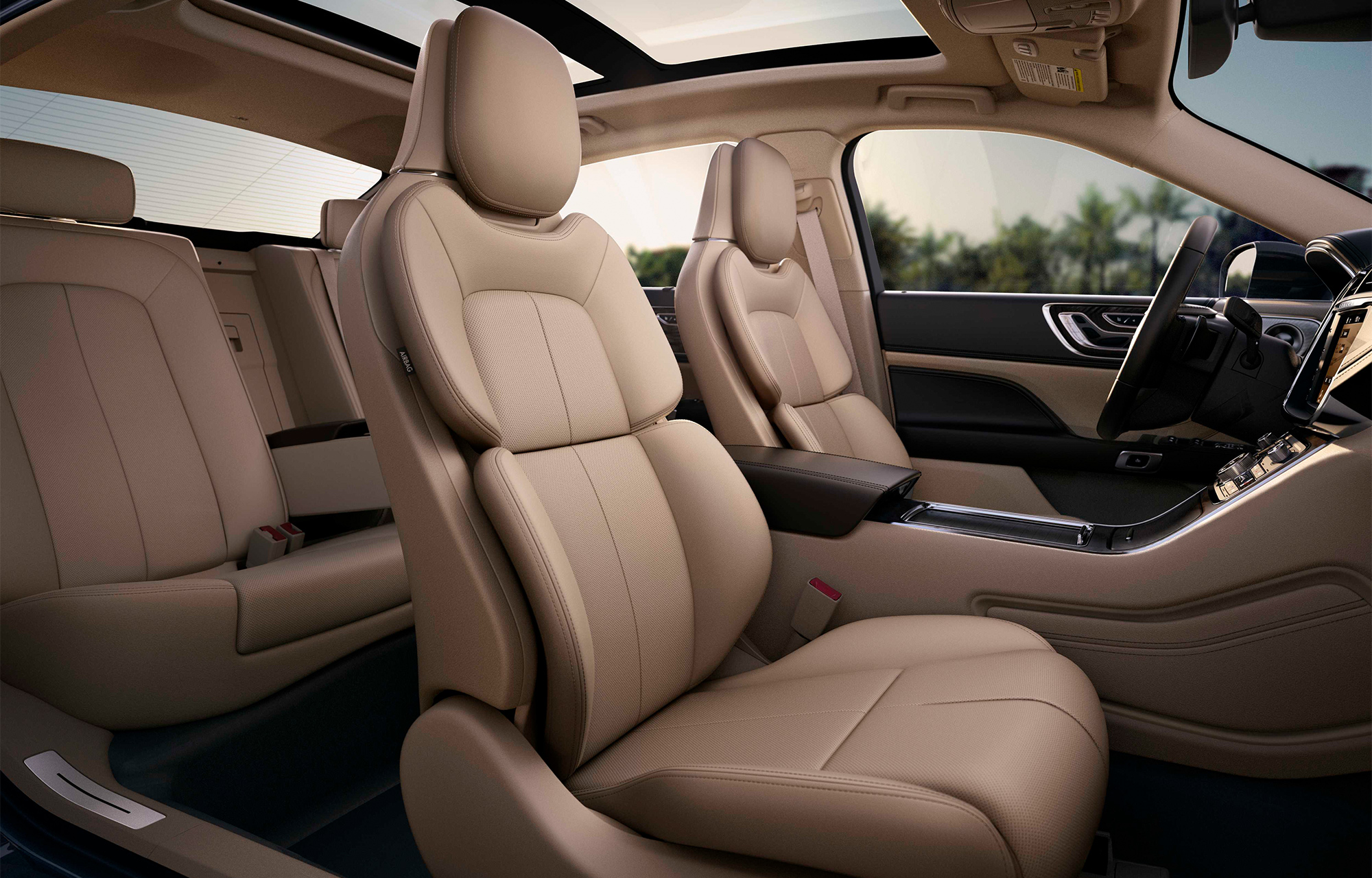
Lincoln - The Inside Story
- What makes Lincoln's luxurious interiors so special? Find out for yourself...
Sliding into the soft embrace of a new luxury vehicle for the first time can often be a sensory overload. The glowing display, the rich aroma of the leather, an array of buttons entreating to be pressed, the delicate wood finishes that cry out to be stroked, the evocation of a sense that this is a unique place, unlike any other. The enhanced feeling of wellbeing that washes over you as you close the door with a satisfying clunk and separate yourself from the outside world and cocoon yourself in a vehicle that becomes an extension of you, what is known as haptic perception.
To get a better understanding of materials close at hand, shutting one’s eyes allows the sense of touch to be more intense, and determine minuscule changes in the materials surface. This is because the seemingly simple process of touch, (also called tactile perception) considered one of the five traditional senses, is in actuality a complex series of modalities that include pressure, skin stretch, vibration and temperature, that feedback information from receptors via sensory nerves, through tracts in the spinal cord and finally into the brain. This complex procedure includes haptic perception which can be best described as active exploration of the world adjacent to one’s body. But why does it feel more intense when we close our eyes? The reduction of another sense is the obvious answer, but the somatosensory system (the mechanism our brain uses to evaluate touch) is different to the other senses – the receptors for these are clustered in the head, the touch receptors are scattered throughout the skin and muscle tissue conveying their message through the spinal cord.
As much as we perceive things visually or acoustically, if we want to learn about something tactilely, there is an urge to reach out and stroke the dog’s fur, rub the material, or the satisfying feeling of pushing a button. Touch is the sense that brings control, we can push, stroke, swipe, block, manoeuvre, grab, shake — it is the most powerful of our senses.
Acquiring the finest leathers and maintaining its premium quality
So where does one start when ensconced in the plush surrounding of a Lincoln? Touching the soft, supple leather? What constitutes this fine accoutrement that makes it so rewarding to touch? Where does it come from and how is it selected? One of the leathers used in all Lincoln models including the Continental and MKZ comes from the west coast of Scotland. From a town outside Glasgow called Bridge of Weir. The company’s highly sought after products are regarded as one of the most environmentally low-carbon leathers, Bridge of Weir uses a unique organic tanning method that is free of chromium. This creates a product that is recyclable at the end of its lifecycle, and by-products that are environmentally sustainable through the tanning operations and free of artificial embossing — which highlights the natural grain inherent in every hide.
Bridge of Weir has developed leather specifically for Lincoln, using specific colours, grains and finishes and created a unique portfolio of four trend groups: Abstract, Dream, Minimalism and Principles.
But what separates the leather used in Lincoln from its competitors? The creation of the perfect leather is a complex and time consuming process that can be broken down into the 13 following stages.
- Liming - After being soaked, the hair and epidermis is removed by treating hides with a mixture of sodium sulphide and lime solutions.
- Fleshing - Removal of any fat still adhering to the back of the hide.
- Splitting - The hide is split into two layers. The grain layer (top) is used in the manufacture of Bridge of Weir Leather. The flesh split (bottom) is sold to other manufacturers for the production of suede, or to the food industry as a source of collagen.
- Tanning - After de-liming and pickling to make the hide more receptive, the hides are tanned to stabilise the collagen fibres and prevent its decay. This can be done either using a solution of recyclable chromium salts producing 'wet blues' or various organic solutions producing 'wet whites'
- Selection - The tanned hides undergo a mechanical process called sammying to remove excess water. The hides are then hand selected into quality grades based on the numbers and location of the naturally occurring characteristics associated with the finest quality hides.
- Shaving - The hides are mechanically shaved to give a uniform substance.
- Dyeing - Hides are dyed in stainless steel drums. Fine oil emulsions are also added at this stage to lubricate the fibres and influence the final softness of the leather.
- Drying - After the addition of natural oil emulsions to lubricate and soften the leather, the hides are either stretched on large frames or vacuum dried.
- Surface coating - Once trimmed, dependent on customer requirements, the initial application of surface pigment is applied by machine roller coating. The final protective coats are applied by machine spraying.
- Finishes & Patina - Different textures designed to enhance the leather's grain surface can be applied by engraved rollers.
- Milling - After surface finishing, the hides are softened by tumbling them for several hours in rotating drums.
- Final Inspection - Each hide is individually checked for quality after processing. If approved, the area is measured electronically prior to despatch.
- Cutting - Leather cutting is a highly skilled job. As leather is a natural material, the aim is to keep wastage to a minimum while preserving all the natural character of the hide in the piece being made.
This final stage is the most critical. Cutting leather is therefore a highly skilled job. The cutter must appreciate what characteristics of the leather are desired in each panel and must therefore consider where each panel fits into the final design of the chair, seat or sofa, in order to make the final product. As no two hides are exactly the same. Characteristic marks of the hides' natural origin are healed scars, neck growth marks, veins, abrasions and areas of different fibre density or hair pore structure will impact immediately on which hides will and won’t be initially selected for the following stages. These occur in all hides, however their numbers and severity differ from hide to hide. Like the grain in timber every hide is unique, not faults but the signatures of one of the most desirable aspiration materials the world over.
The leather is then subjected to many quality tests before being sent to fit in the interior of your Lincoln. So next time you take your place in a new Lincoln’s driver’s seat. Take a moment, close your eyes and touch the soft leather seats and appreciate the level of detail that’s at your fingertips.